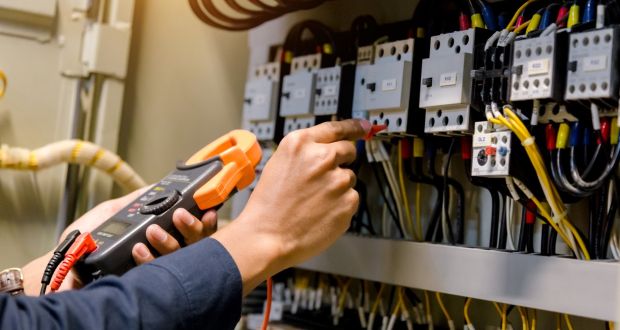
Pinch Analysis for Maximising Energy and Resource Efficiency
“Pinch Analysis has led to utility savings in the range of 10 – 60%, and capital savings of up to 30%.”
1. Waste heat recovery provides the No. 1 energy-saving potential in the industry
Up to 50% of the industry’s thermal energy input is finally lost as waste heat in exhaust gases, cooling water, and on heated surfaces and products [Thermal Energy: Sources, Recovery and Applications. Yatish T. Shah, 2018]. Recovery of thermal energy from waste heat presents the biggest cost-saving opportunity through energy efficiency improvement in the industrial sector.
Opportunity to maximise heat recovery may be missed unless a systematic technique is employed to address heat recovery problems involving multiple processes and equipment.
2. What is Pinch Analysis?
Pinch Analysis (PA) is a systematic tool to maximise thermal energy and resource efficiency through maximum waste heat and resource recovery. PA provides facility and site planners, plant designers and process engineers with practical knowledge, skills and systematic methods for the optimal planning, design and retrofit of processes, facilities and manufacturing sites to maximise the recovery of energy and resources such as water, power and materials; and to minimise costs and emissions.
Practical Pinch Analysis applications in the context of energy audit consist of two key steps, i.e., 1. Setting the minimum energy targets based on process material and energy balances and determination of the upper limit, i.e. the bottleneck or the pinch point for energy recovery, 2. Design or retrofit of heat recovery networks to achieve the minimum energy targets. Pinch Analysis provides energy auditors with a powerful tool to recommend and implement measures and options to maximise energy cost-saving opportunities and minimise emissions during an energy audit.
3. What are the benefits of Pinch Analysis?
Pinch Analysis promotes industrial symbiosis through process integration that has enabled companies to achieve triple-bottom-line benefits of minimised utilities (e.g. thermal energy, electricity, water), minimised costs (operating, maintenance and investment costs) and minimised wastes (CO2, gaseous emissions, water).
Over 7,000 successful Pinch Analysis applications worldwide, including our project experiences show that pinch analysis applications led to potential thermal energy and utility cost savings of between 10 to 60%, and payback periods of less than three years. One of our recent petroleum refinery retrofit project, for example, amassed an annual saving of USD 12 Million.
Real Examples of Triple-Bottom Line Benefits for companies that maximise waste heat recovery:
USD 12.8mil/year on energy savings by Retrofit of Heat Recovery System
USD 4.1mil/year on energy savings by Total Site Heat Integration Retrofit Study
USD 0.75mil/year on energy and water recovery savings
4. Who should conduct Pinch Analysis?
If thermal energy is one of the leading energy costs in a manufacturing site, then Pinch Analysis study should be conducted.
5. Other than installing waste heat recovery at utility boiler/furnace flue gas, what other heat recovery opportunities are there?
Utility boilers/furnaces constitute the energy supply side that provides heat to satisfy process energy demand-side consisting of units as reactors, kilns, separators, evaporators, dryers, heat exchanger network, heaters, coolers and refrigeration systems. Over time, demand for energy supply from boilers/furnaces of a manufacturing site will typically rise due to inefficiencies and ageing equipment. The bulk of rising demand for more heat from boilers typically originates at the core of the process, i.e. at the reactor, followed by separator, process heaters and heat exchangers. If energy audit and heat recovery are concentrated on the boiler (supply side), the significantly larger energy-saving opportunity at the demand side can be lost. Therefore, the process (demand side) needs to be thoroughly audited so that potential energy recovery and efficiency improvement opportunities shall not be missed.
Consider the bigger picture to maximise energy savings
6. We already have heat recovery systems in place. How could we benefit more?
Over the years, plant renovations, expansion, and addition of new equipment product lines may cause existing processes and utility systems to deviate from the optimum operation. Our experience shows that revisiting utility system and considering site-wide and area-wide energy recovery opportunities could lead to ample energy cost-saving potentials.
7. Who can provide Pinch Analysis service?
Our team comprises leading Pinch Analysis experts with over 30 years of experience in conducting R&D and providing consultancy and professional training services covering thermal energy audit, process design, process improvement and retrofit of heat recovery systems for more than 500 national and multinational companies.
The Process Systems Engineering (PROSPECT) research centre where we have developed innovative Pinch Analysis solutions has been Globally Ranked No. 1 in Research on ‘Heat Exchangers, Retrofitting and Design’ in the 2014 Elsevier Scival Spotlight Report. Our globally published work on practical Pinch Analysis applications titled Industrial Implementation Issues in Total Site Heat Integration has been reported by Web of Science, Thomson Reuters as highly cited, top 1% referenced work.
30+Years Experience in Thermal EnergyAudit & Retrofit of Heat Recovery System
500+ National & Multinational Companies Benefited from our Energy Training Workshops
#1 Global Rank in Research ‘Heat Exchanger, Retrofitting and Design’ Elsevier Scival Spotlight 2014
Top 1% referenced and cited work byWeb of Science, Thomson Reuters
8. Are there software tools that can help perform Pinch Analysis?
Optimal Heat is a software that can assist engineers design cost-effective heat exchanger networks in maximising heat recovery using Pinch Analysis technique.
9. Where can I learn more about Pinch Analysis?
We provide online and face-to-face Thermal Energy Recovery Technologist (TERT) training in the region for those who would like to learn more on Pinch Analysis from beginners to advanced level.
References
- Klemes, J. J., Varbanov, P. S., Wan Alwi, S. R., Manan, Z. A. (2018), Sustainable Process Integration and Intensification: Saving energy, water and resources. 2ndEdition, De Gruyter, Germany. ISBN: 978-3-11-053535-8. https://www.degruyter.com/view/title/526753
- Z. A. (2006), Consider the Bigger Picture to Maximise Energy Savings, The Jurutera, March 2006.
- Manan, Z. A. (2004). Maximizing energy efficiency and minimizing environmental emissions in the process industry using thermal pinch analysis. ASEAN Journal of Chemical Engineering. 4 (2): 32-39. https://jurnal.ugm.ac.id/AJChE/article/view/50836
- Manan, Z. A. and Lim, F. Y. (2004). Maximising utility savings through appropriate implementation of combined heat and power scheme. Jurnal Teknologi, 41(A), 53-62. http://eprints.utm.my/id/eprint/1919/1/JTDIS41A05.pdf
- Liew, P. Y., Lim, J. S., Wan Alwi, S. R., Manan, Z. A., Varbanov, P., Klemes, J. J. (2014). A retrofit framework for Total Site heat recovery systems, Applied Thermal Engineering. 135: 778-790. https://www.sciencedirect.com/science/article/abs/pii/S0306261914003304
- Lai Y.Q., Manan Z.A., Wan Alwi S.R. (2018). An enhanced tool for heat exchanger network retrofit towards cleaner processes. Chemical Engineering Transactions. 63:487-492. https://www.cetjournal.it/index.php/cet/article/view/CET1863082
- Muhammad, T. J., Wan Alwi, S. R., Manan, Z. A. (2009), Cost-Effective Retrofit of a Palm Oil Refinery using Pinch Analysis. Jurnal Teknologi. Series E, 51: 29-40. http://eprints.utm.my/id/eprint/9989/
- Munir, S. M., Manan, Z. A., Wan Alwi, S. R. (2012). Holistic carbon planning for industrial parks: a waste-to-resources process integration approach. Journal of Cleaner Production. 33: 74-85. https://www.sciencedirect.com/science/article/abs/pii/S0959652612002491
Updated at January 12, 2021 by Optimal Systems Engineering
Make an Inquiry Here